- Aloe Vera Powder Plant
- Coconut Milk Powder Plant
- Egg Powder Plant
- Fish Protein Hydrolysate Powder Plant
- Fruit Powder Plant
- Ice-Cream Mix Powder Plant
- Lactose Powder Plant
- Malt Powder Plant
- Microcrystalline Cellulose Powder Plant
- Non-Dairy Creamer Powder Plant
- Pectin Powder Plant
- Soy Milk Powder Plant
- Sugarcane Juice Powder Plant
- Tamarind Extract Powder Plant
- Zinc Sulphate Powder Plant
- Zero Liquid Discharge System
Fluid Bed Dryers, Granulators & Coolers
Working Principal
A fluid-bed system is a Dryer in which flow of wet powder, granular or flakes material is
conveyed over a perforated bed. Hot drying air is blown through the holes of a perforated
plate. The wet solids are lifted from the bottom and causes the solids to behave as a fluid.
The air velocity is adjusted (carefully calculated) to keep the moving layer of material
fluidized. Very high heat and mass transfer rates are obtained as a result of the intimate
contact between individual particles and the fluidizing gas.
Properly used, fluidized bed drying provides an efficient solution for the gentle and even
drying of your product.
Different types of Designs are available in Fluid Bed Dryers and in Open Cycle and or Closed Cycle viz.
- Static Fluid Bed Dryer
- Vibratory Fluid Bed Dryer.
- Internally Heated Fluid Bed Dryers
- Internally Stirred Fluid Bed Dryers
- Aero-dynamic Rotating Fluid Bed Dryers.
Based on the required powder properties and feed liquid rheology suitable type of Dryer is supplied by us.

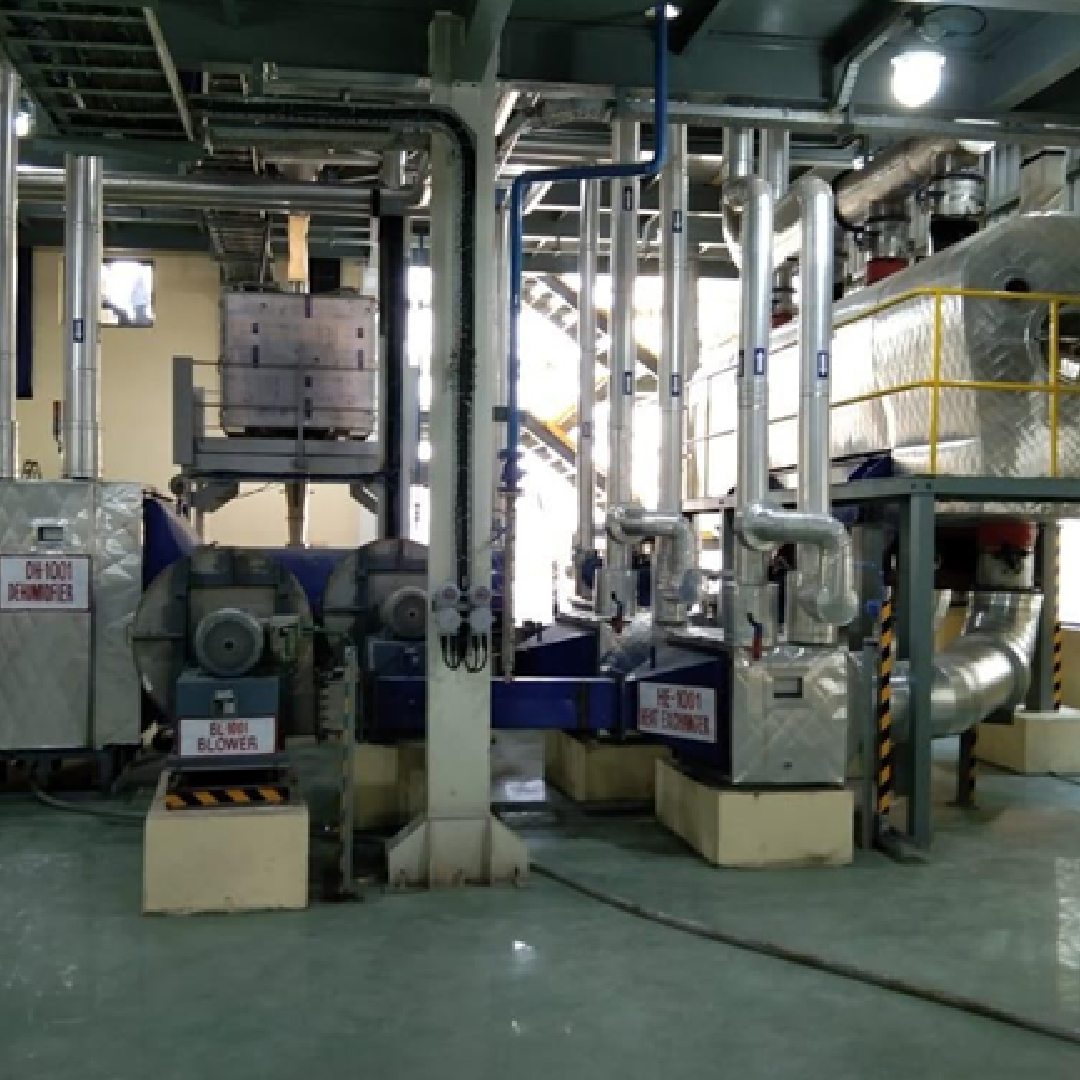
Features of RAYGM Fluid Bed Dryers:
- Carefully designed thermodynamic paste mixers with partial removal of moisture before feeding to main fluid dryer.
- Relatively simple in operation.
- Carefully chosen thermodynamic conditions suitable for materials to prevent degradation or attrition of the product.
- Recycling of fines generated to main feed for further mixing, agglomeration and uniform product qualities.
- Continuous operation and suitable for sticky materials with a wide particle size distribution.
- Drying gas temperature up to 700 °C and product temperatures up to 300 °C are achieved.
Benefits of RAYGM Fluid Bed Dryers:
- Controlled Temperatures, residence time, air flow lowers Drying Cost on per kg basis.
- Products are dried uniformly.
- Can handle variety of materials like pastes, Crystalline powders, Chemicals, Pharmaceuticals.
- Due to fairly automatic process low manpower is required which ultimately lowers Drying Cost on per kg basis.
- Using submerged heating through conduction volume of air is lowered and very effective for recovering expensive solvents. Less Airflow means effective recovery of Solvents and lower Drying Cost on per kg basis.
- In same system Agglomeration, Drying, Cooling can be done lowering the foot print and manpower requirement. Lower capital cost, and lower Drying Cost on per kg Basis of Product.
RAYGM Fluidized-bed Granulation Fluidized Bed Coater

Fluidized bed coating technology is often combined with other microencapsulation technology, such as Spray Drying. One of the advantages of fluid bed technology is its large selection of coating materials, as they can be either hydrophilic or hydrophobic in nature, solvent-mediated or non-solvent formulations. Coating thickness can also be easily controlled to create the desired wall structure. Fluidized bed technology provides another option for double encapsulation technology. For instance, Fluidized Bed Coating can be used as fluidized bed coater to apply a Gum Arabic coat to spray-dried capsules prepared from modified starch, maltodextrin, or cyclodextrin aimed at inhibiting oxidation. Also, can be utilized this approach to coat solid lipids such as carnauba wax, paraffin or bees wax, and stearic acid onto the surfaces of milk protein-based microcapsules with entrapped oil, in order to add a moisture barrier. Costing hydrogenated soybean oil onto microencapsulated fish oil powders using a fluidized bed coater to facilitate flowability and a neutral taste.
RAYGM Fluidized-bed Granulation

Fluidized-bed granulation procedure, in contrast to extrusion, is much more advantageous in that it introduces many more process parameters that could potentially influence and control the properties of the product. As liquid binder is introduced, typically via spray nozzle, particles agglomerate in the fluidized bed into desired size granules. The technique is extremely flexible and could easily be adopted for the mass production of bio sorbents. Different type of cross-linking can be accomplished during the process with the addition of a suitable chemical (e.g., dimethylolethylene urea).
RAYGM Hybrid Fluidized Bed Dryers for Food and Pharmaceutical Products
Hybrid fluidized bed driers incorporating a heat pump drying mechanism have been developed as shown for food and pharmaceutical products. The drying chamber receives wet material and discharges dried product through the product inlet and outlet ducts. The desired operating temperature is obtained by adjusting the condenser capacity, while the required air humidity is maintained by regulating the compressor capacity via frequency control of the motor speed. This set-up can produce drying temperatures from –20°C to 60°C and air humidity spanning 0% to 90% With these features, heat-sensitive food materials can be dried under convective air and or freeze-drying conditions. It is also possible to sequence these two operations (convective and freeze drying). This will be advantageous for drying of food and bioproducts since freeze drying causes minimal shrinkage but produces low drying rates while convective air drying can be applied to enhance drying rates. Therefore, a combination of drying processes, e.g. freeze drying at –5°C followed by convective drying of 20–30°C, enables the control of quality parameters such as porosity, rehydration rates, strength, texture, colour, taste, etc. New hybrid fluidized bed drying offers a better product quality but at higher cost.

RAYGM Fluid Bed Dryers, Granulator, Coater cum Coolers Design Range and Manufacturing Capacity
Design |
|
Feeding Arrangement |
|
Application |
|
Area |
|
Configuration |
|
Material |
|
Heating Methods |
|
Air-Flow Direction |
|
Product Recovery |
|
Emission Control |
|
Automation & Controls |
|
Option Features Depending on Product Properties. |
|
Partial Product Applications of RAYGM Fluid Bed Dryers.
Cut Vegetables, Extruded Agrochemicals Granules, Extruded Insecticides, Herbicides, Salts, Dairy Products, Paints and Pigments, Pharmaceuticals like Carboxymethyl Cellulose, Lactose, Dextrose, Minerals like Sand, quartz sand, silica sand, gypsum, slag sand, limestone, kaolin, potash, phosphates, coal, mineral ores etc.