- Aloe Vera Powder Plant
- Coconut Milk Powder Plant
- Egg Powder Plant
- Fish Protein Hydrolysate Powder Plant
- Fruit Powder Plant
- Ice-Cream Mix Powder Plant
- Lactose Powder Plant
- Malt Powder Plant
- Microcrystalline Cellulose Powder Plant
- Non-Dairy Creamer Powder Plant
- Pectin Powder Plant
- Soy Milk Powder Plant
- Sugarcane Juice Powder Plant
- Tamarind Extract Powder Plant
- Zinc Sulphate Powder Plant
- Zero Liquid Discharge System
Spray Dryers
Spray-drying is the
transformation of a pumpable feed from a fluid state into a dried particulate form by
spraying the feed into a hot and or dehumidified drying medium.
The liquid to be dried is generally preconcentrated by evaporation to economically reduce
the water content. The concentrate is then introduced as a fine spray or mist into a tower
or chamber with heated air. As the small droplets make intimate contact with the heated air,
they flash off their moisture, become small particles, and drop to the bottom of the tower
and are removed. The advantages of spray drying include a low heat and short time
combination which leads to a better-quality product.
Spray Dryers are divided into several types by operation process as below.
Based on Atomization Systems Spray Dryers are divided into
- High Speed Centrifugal Atomization Dryers (Atomization by Rotation Energy)
- High Pressure (Hydraulic) Nozzle Atomization Dryers (Atomization by Pressure Energy)
- Pneumatic Nozzle (Air / Inert Gas) Atomization type Dryers. (Atomization by Kinetic Energy)
Based on the required powder properties and feed liquid rheology suitable type of Dryer is supplied by us.
Benefits and Uses of RAYGM Spray Dryers.
- Product quality and properties can be effectively controlled and maintained through the entire drying operation.
- Thermolabile products/ pharmaceuticals can be dried at atmospheric pressure and low temperature.
- Product degradation or fire hazard is avoided by selection of right drying conditions. No sticking of materials in Drying Chamber by providing right drying conditions and this is unique to us.
- It is employed in enhancing solubility and dissolution rates of poorly soluble drugs by formation of pharmaceutical complexes or via the development of solid dispersion thus increasing bioavailability.
- It is equally used in the preparation of matrix microcapsule containing drug substances and a biodegradable polymer in order to obtain controlled drug release formulation.
- Spray dryer permits high- tonnage production in continuous operation adaptable to conventional PLC control (Programmable Logic Controller) and it is relatively simple to operate.
- Feedstock in solution, slurry, emulsion, paste, and melt form can be dried if pumpable.
- Corrosion problem is minimal and the selection of materials of construction of spray dryer is simplified since the dried material comes in contact with the equipment surfaces in an anhydrous condition.
- Spray dryer produces dry powder particles of controllable particle size, shape, form, moisture content, and other specific properties irrespective of dryer capacity and heat sensitivity.
- Spray dryer handles a wide range of production rates and provides extensive flexibility in its design that is product specification are readily met through the selection of appropriate spray dryer design and its operation from a wide range of available design.
- It is easy to clean after use. Manual or automatic system are supplied upon request.
- It has a high thermal efficiency. Outlet temperatures are lowered using giving optimum residence time and not lowering the sizing of the system. Option for recovering heat from exhaust gases is offered with well researched technologies.
High Speed Centrifugal Atomization Dryers (Atomization By Centrifugal Force of Rotation)
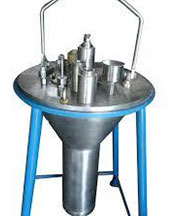


Rotary atomizer uses the energy of a high speed-rotating wheel to divide bulk liquid into droplets. Feedstock is introduced at the centre of the wheel, flows over the surface to the periphery and disintegrates into droplets when it leaves the wheel. Particle produced in this type of Atomizer is with wide range and mainly dependent on the Rheology of the feed slurry.
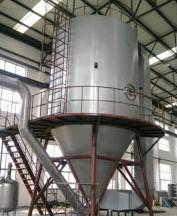


2 High Pressure (Hydraulic) Nozzle Atomization Dryers (Atomization by Pressure Energy)

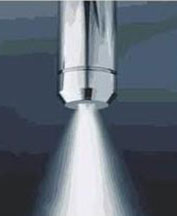
Pressure nozzle is the most commonly used atomizer for spray drying. Nozzles generally produce coarse, free flowing powders than rotary atomizers. Pressure nozzles used in spray drying are called “vortex” nozzles because they contain features that cause the liquid passing through them to rotate. The rotating fluid allows the nozzle to convert the potential energy of liquid under pressure into kinetic energy at the orifice by forming a thin, high-speed film at the exit of the nozzle. The range of operating pressure range for pressure nozzles used in spray drying is from about 25 Bar to 300 Bar.



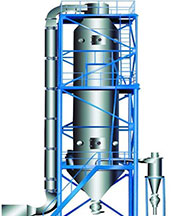
3 Two Fluid Nozzle (Air / Inert Gas) Atomization type Dryers. (Atomization by Kinetic Energy)
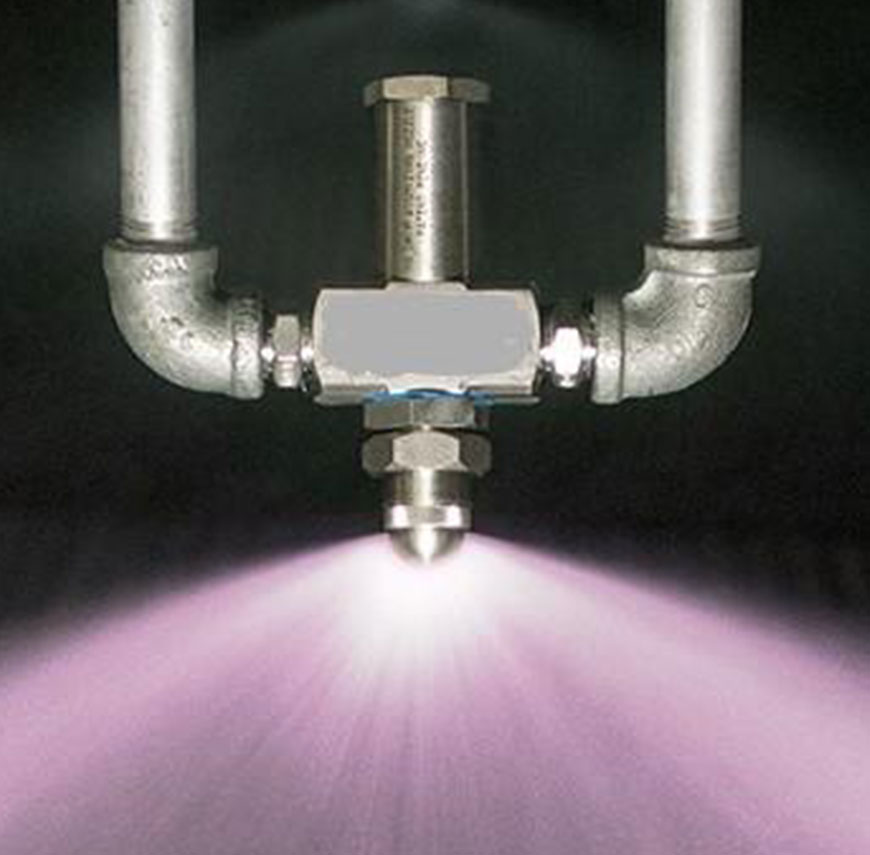
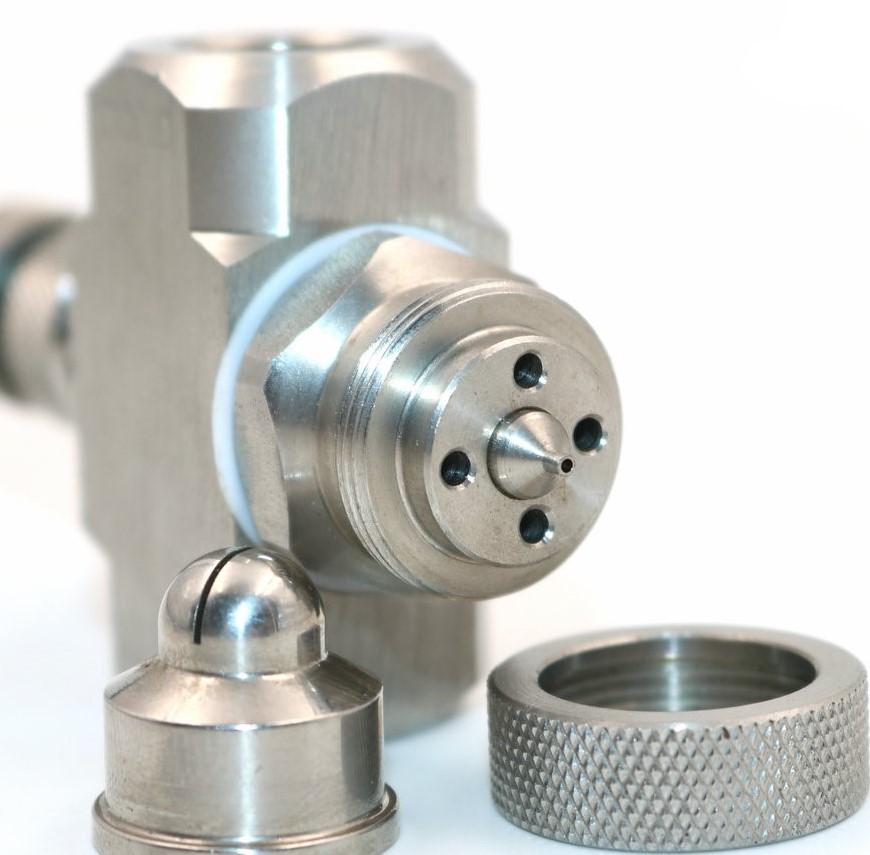
Liquid feedstock and compressed air (steam) are combined in a two-fluid nozzle. The design
utilizes the energy of compressed gas to atomize the liquid. Two advantages of the two-fluid
nozzle are its ability to produce very fine particles and to atomize highly viscous feeds.
The range of operating air (gas) pressure range for two fluid nozzles used in spray drying
is from 0.3 to about 8 Bar of gas Pressure.
Compressed air usually is the atomizing gas but many other gases, including steam, oxygen
and methane, can be used. The nozzle provides two advantages: it can spray more-viscous
material, and enables the average drop size to be adjusted independent of liquid flow. The
downside is that the energy input is much higher per mass of material sprayed. The hidden
cost of supplying the compressed air is easily overlooked.

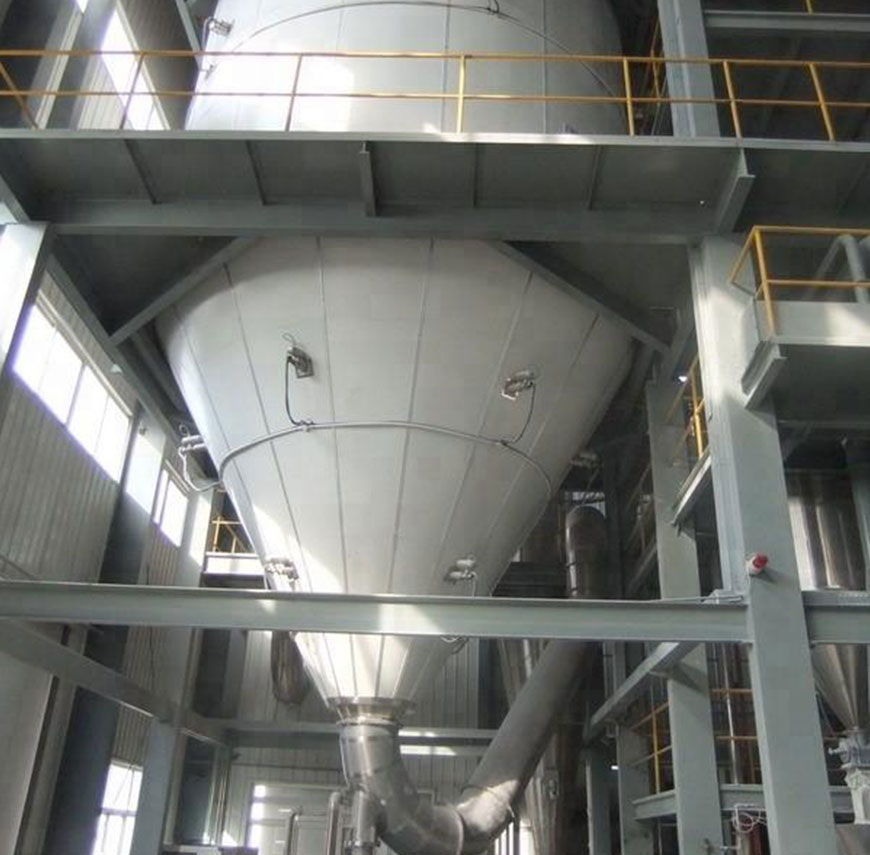
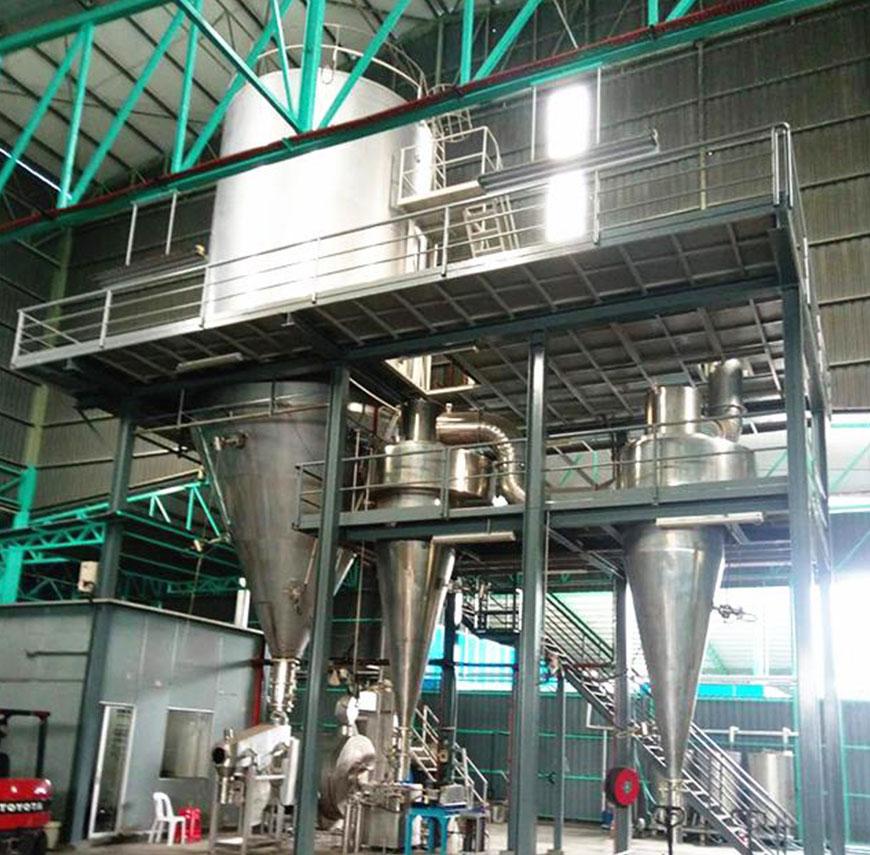
Special types of Dryers
4 RAYGM Two and Three-stage Drying
In standard, single stage spray drying, the rate of evaporation is particularly high in the
first part of the process, and it gradually decreases because of the falling moisture
content of the particle surfaces. In order to complete the drying in one stage, a relatively
high outlet temperature is required during the final drying phase. The outlet temperature is
reflective of the particle temperature and thus heat damage.
Consequently, the two-stage drying process was introduced which proved to be superior to the
traditional single stage drying in terms of product quality and cost of production.
The two stage Dryer consists of a spray Dryer with an external vibrating fluid bed placed
below the drying chamber. The product can be removed from the drying chamber with a higher
moisture content, and the final drying takes place in the external fluid bed where the
residence time of the product is longer and the temperature of the drying air lower than in
the spray dryer.
This principle forms the basis of the development of the Three-stage Dryer. The second stage
is a fluid bed built into the cone of the spray drying chamber. Thus, it is possible to
achieve an even higher moisture content in the first drying stage and a lower outlet air
temperature from the spray dryer. This fluid bed is called the integrated fluid bed. The
inlet air temperature can be raised resulting in a larger temperature difference and
improved efficiency in the drying process. The exhaust heat from the chamber is used to
preheat the feed stream. The third stage is again the external fluid bed, which can be
static or vibrating, for final drying and/or cooling the powder.
The results are as
follows:
- higher quality powders with much better rehydrating properties directly from the Dryer
- lower energy consumption
- increased range of products which can be spray dried
- smaller space requirements
- Improved particle size with dust free powder.
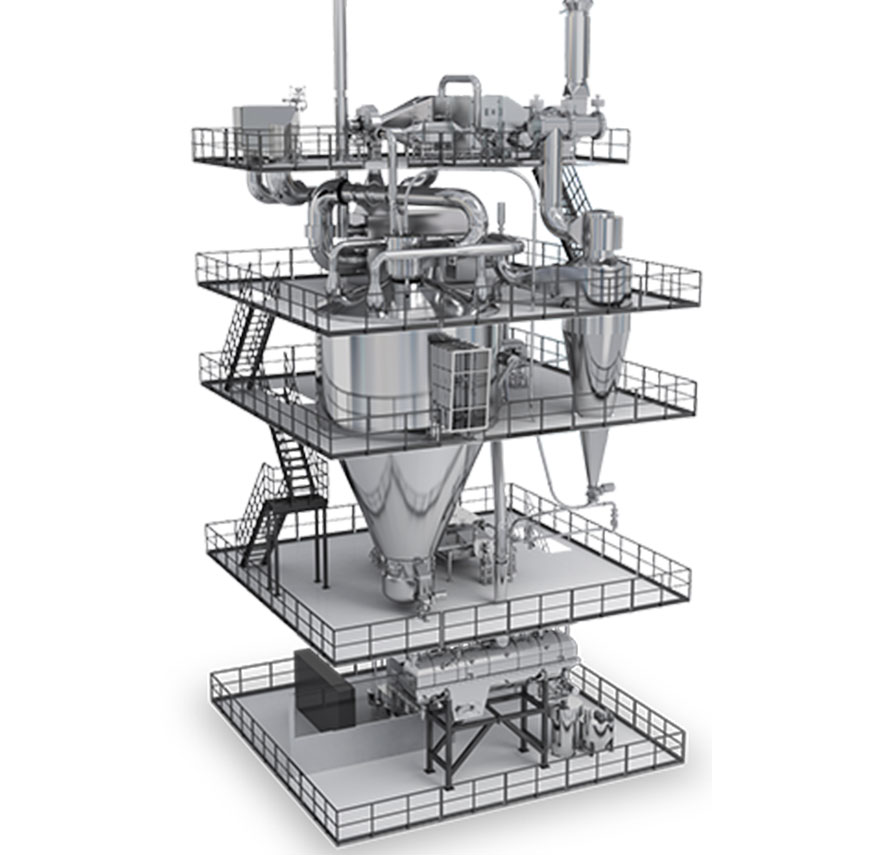

5 RAYGM Closed Loop Spray Dryer
The spray dryer with closed circulation drying system works under enclosed environment. The
drying requires inert gas which is generally nitrogen.
The closed circulation drying system is mainly used for drying of material containing
alcohol or flammable and combustible solvent or material which can be easily oxidized so
that it should not contact the air. By filling with nitrogen and some other inert gases,
this dryer can protect the material from air.


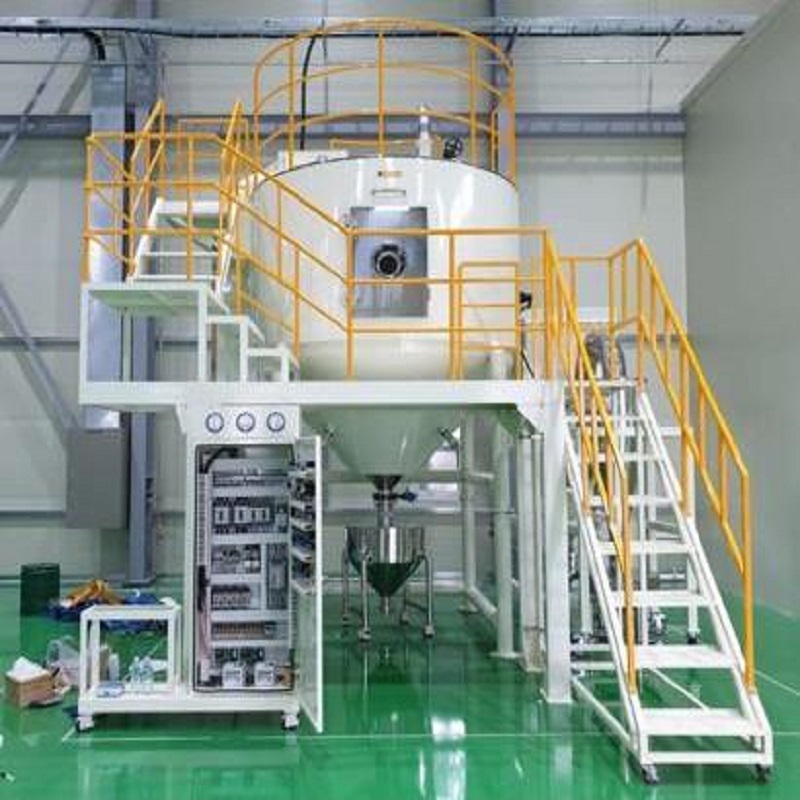
5 Types of spray dryer systems on the basis of the type of flow
RAYGM Co-current flow dryer
In the co-current flow dryer, the spray is directed into the hot air entering the dryer and both pass through the chamber in the same direction. Spray evaporation is rapid and the temperature of the drying air is quickly reduced by the vaporization of water.
RAYGM Counter-current flow dryer
In this dryer design, the spray and the air are introduced at opposite ends of the dryer, with the atomizer positioned at the top and the air entering at the bottom. A counter-current dryer offers more rapid evaporation and higher energy efficiency than a co-current design. Because the driest particles are in contact with hottest air, this design is not suitable for heat-sensitive products.
RAYGM Mixed flow dryer
Dryers of this type combine both co-current and counter current flow. In a mixed flow dryer, the air enters at the top and the atomizer is located at the bottom. Like the counter-current design, a mixed flow dryer exposes the driest particles to the hottest air, so this design is not used with heat-sensitive products.

Partial Product Applications of RAYGM Spray Dryers
Design |
|
Application |
|
Capacity |
|
Configuration |
|
Material |
|
Heating Methods |
|
Temperature Range |
|
Air-Flow Direction |
|
Product Recovery |
|
Emission Control |
|
Automation & Controls |
|
Option Features Depending on Product Properties. |
|
Partial Product Applications of RAYGM Spray Dryers
Degree of application decides the importance of process. Spray drying technology is widely
applied in Chemicals, Pharmaceutical, Food, Biomedical as well as Mineral, fields.
Pharmaceutical products like antibiotics, enzymes, vitamins, yeasts, vaccines,
plasma,
Algae, antibiotics and moulds, bacitracin, penicillin, streptomycin, sulphathiazole,
tetracycline, dextran, enzymes, lysine (amino acids), pharmaceutical gums, sera, spores,
tableting constituents, yeast products, tannin products, excipients, Co processed
Excipients, Gum Arabic etc.
Dyestuffs like Acid / Metal Complex Dyes, Reactive Dyes, Disperse Dyes, Vat Dyes,
various
Food, Paint and Natural Pigments Etc.
Detergents (Household and Laundry) and Surfactants used in Chemical, Agrochemical,
Biotechnology, Food Industry Etc.
Food Processing like Tea, Coffee, Food Flavours, Food Colours (Synthetic and
Natural),
Pectin (Hyaluronic Acid), Biopolymers, Enzymes, Milk and By-products, Egg Products, Proteins
(Boven and Veg), Fruit (Apple, Banana, Blackberry, Blueberry, Cherry, Coconut, Cranberry,
Date, Dragon-fruit (or Pitaya), Durian, Grapefruit, Guava, Jackfruit, Lemon, Lime, Lychee,
Mango, Watermelon, Orange, Papaya, Peach, Pear, Plum, Pineapple, Pomegranate, Raspberry,
Strawberry, Tamarind, Tomato) Powders.
Agrochemicals Like Sulphur WDG, Mancozeb, Zinc Sulphate, Nitrates, Ammonium salts,
Phosphates, Ortho-Phosphates Etc.
Minerals like Ceramics, Kaolin Clay, Bentonite Clay, Aluminium oxides, Carbides, Iron
Oxides
etc.