- Aloe Vera Powder Plant
- Coconut Milk Powder Plant
- Egg Powder Plant
- Fish Protein Hydrolysate Powder Plant
- Fruit Powder Plant
- Ice-Cream Mix Powder Plant
- Lactose Powder Plant
- Malt Powder Plant
- Microcrystalline Cellulose Powder Plant
- Non-Dairy Creamer Powder Plant
- Pectin Powder Plant
- Soy Milk Powder Plant
- Sugarcane Juice Powder Plant
- Tamarind Extract Powder Plant
- Zinc Sulphate Powder Plant
- Zero Liquid Discharge System
RAYGM High Speed Rotary Atomizer.
The High-Speed Rotary Atomizer is a heart and key component in a Spray Dryer Plant. 80% of the powder properties are dependent on the Rotary Atomizer and Air Distributor in the Spray Drying Plant. Design, Selection, Installation and working of high-Speed Rotary Atomizers defines the reputation of Spray Dryer and powder produced through it.
Features of RAYGM Rotary Atomizer
- ASTM Grade materials with complete understanding of metallurgy required for different components.
- Atomizers are designed with High temperature, self-aligning bearings.
- Designed with high reliability for long terms operations and avoid unnecessary downtime in production due to design or materials defect. Every Component tested and verified to standard.
- High centrifugal force available with high tip (rotation) speed of the wheel (up to 200 meter/sec).
- Correct Wheel Geometry and distribution configuration designed according to the product specification in order to avoid deposits, clogging, Vibrations of wheel or undesired sticking of particles in Spray Chamber and further darkening of particles in the final product.
- Our Atomizers and designed for Flexibility in operation to handle a wide range of products in a controllable operation in order to produce any type of desired powder.
- Supplied with Inbuilt VFD Panel for Jerk Free Operation.
- Analysed and designed to overcome critical speed of the shaft. FEA analysis if performed for the same.
Benefits of RAYGM Rotary Atomizer
- Rotary atomizer is flexible in operation. By Changing Speed and or Wheel Geometry different particle sizes from 5 up to 250µ can be produced, more interestingly with different Bulk densities.
- Liquid feed systems operate at a relatively low pressure due to the atomization energy is supplied by the wheel’s high speed.
- Special design for handling large quantities of abrasive and non-abrasive liquids / Fluids.
- Can handle highly viscous and or concentrated slurry or fluids.
- Able to operate where clogging due to rheology of the feed material would be a problem for spray nozzle systems.
- Can handle products with Partial crystallized slurry.
- Can be equipped with carefully designed and analysed different wheel designs giving different powder characteristics and bulk density for same product.
- Can operate with higher solid content in the feed, therefore better economy and less drying cost per kg of product.
RAYGM Rotary Atomizer Models
Model No. | Wheel Diameter (mm) | Liquid Feed Rate | Connected Power |
---|---|---|---|
HSA - 60 | 58 | 10 Litre/Hr | ≤ 0.37 Kw |
HAS - 100 | 98 | 100 Litre/Hr | ≤ 1.1 KW |
HSA - 160 | 158 | 1000 Liter/Hr | ≤ 7.5 KW |
HAS - 200 | 205 | 3000 Litre/Hr | ≤ 22 KW |
HAS - 250 | 252 | 5000 Litre/Hr | ≤ 37 KW |
HSA - 300 | 301 | 6000 Litre/Hr | ≤ 75 KW |
HAS - 350 | 349 | 10000 Litre/Hr | ≤ 110 KW |
Powers indicated are provisional and with higher viscosities. We provide power after careful consideration of requirements, Liquid rheology and product properties desired. Optimization of the drying cost is ultimate goal.
RAYGM Rotary Vacuum Dryer Design Range and Manufacturing Capacity
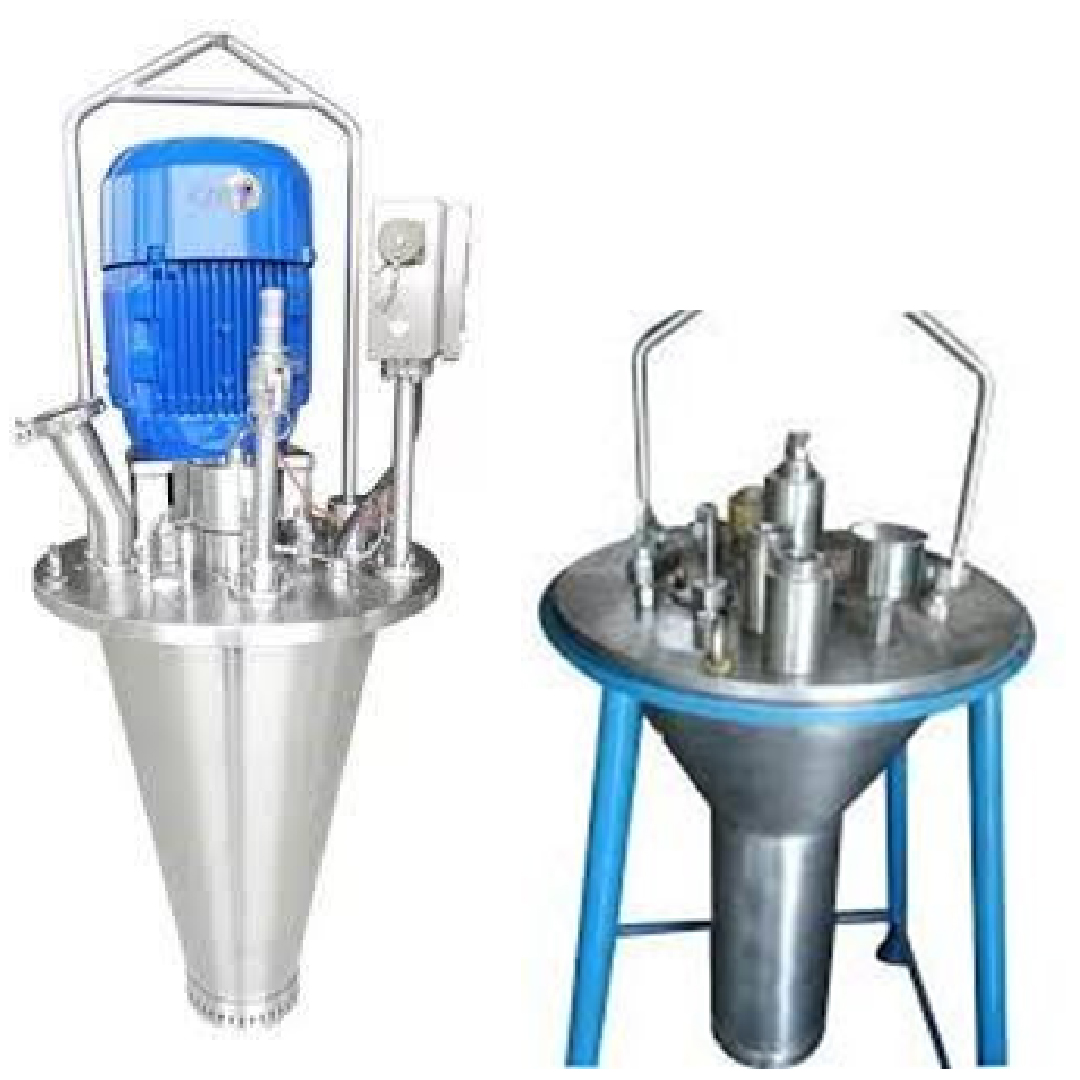
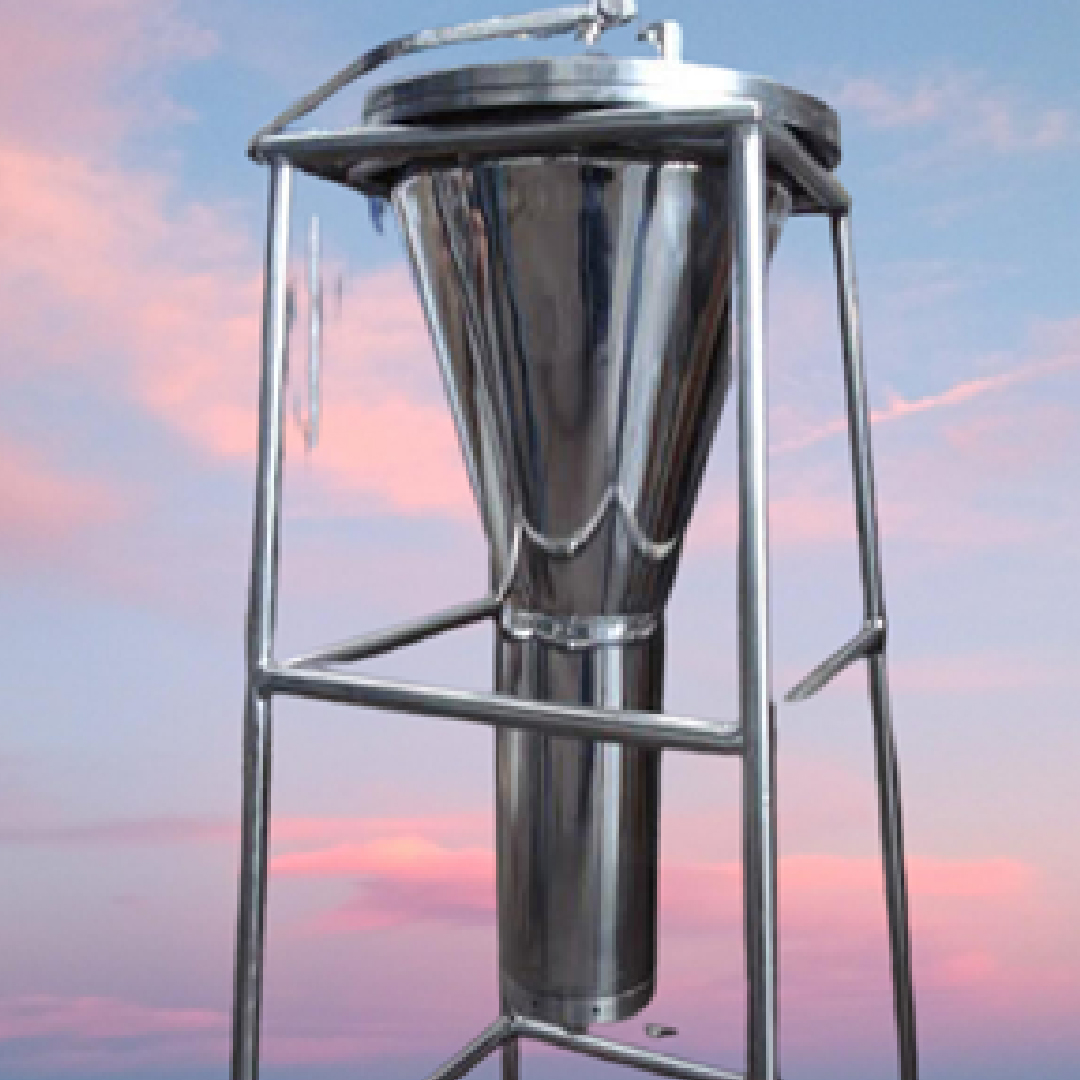
RAYGM Rotary Vacuum Dryer Design Range and Manufacturing Capacity
Depending on type of the Slurry, rheological properties of slurry and properties of product desired different types of wheels are supplied us, viz.
- Standard Wheel with radial openings with or without inserts.
- Staggered Opening Wheel
- Double Decker Wheel
- Pin Wheel
- Curved Vane Wheel
- Slotted Opening Wheel
- Umbrella type Wheel etc
Atomizer Wheel Materials.
- Stainless Steel 430, 304, 316, Hastelloy, with or without inserts.
- Duplex 32205, Super Duplex Steel 2507 with or without Inserts.
- Hastelloy C276 and other families with or without inserts.
- Inconel 600, 825 etc. with or without inserts.
- Titanium Gr. 2 and 12 etc. with or without inserts.
- Stainless steel.
- Alumina
- Silicon Carbide (SiC)
- Boron Carbide hot pressed
- Tungsten Carbide